Exploring the Art and Science of Tool Engineering & Digital Manufacturing
May 29, 2024 2024-06-01 2:09Exploring the Art and Science of Tool Engineering & Digital Manufacturing
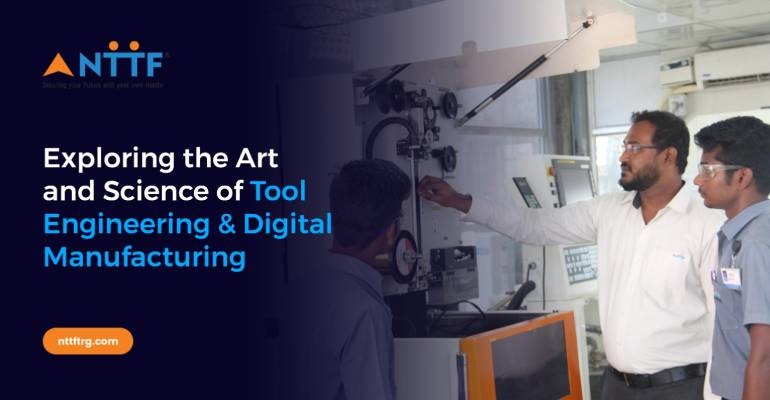
- Introduction
- The Evolution of Tool Engineering
- Digital Manufacturing: The New Frontier
- The Convergence of Tool Engineering and Digital Manufacturing
- NTTF: Bridging the Gap Between Tradition and Innovation
- Integration in Education and Training
- The Future of Tool Engineering & Digital Manufacturing
- Charting a Future in Tool Engineering & Digital Manufacturing
In today’s technologically advanced era, the fields of Tool Engineering & Digital Manufacturing stand at the forefront of industrial innovation. These disciplines meld the precision of engineering with the latest digital technologies, reshaping the way we create and manufacture products.
Are you looking to build a career in the Tool Engineering and Digital Manufacturing industry in India? And what better way to develop the necessary skills than a diploma from a well-known technical training institution like Nettur Technical Training Foundation (NTTF)?
From in-depth analyses of educational programs like the diploma in tool engineering to essential skills gained through CNC machine operator course, join us as we uncover the complexities and innovations driving this exciting industry forward.
The Evolution of Tool Engineering
Tool engineering has historically been a cornerstone of manufacturing, involving the design, creation, and maintenance of tools that enable production. At its core, Tool Engineering encompasses the manufacturing of Press Tools, Moulds, Jigs and Fixtures, and Gauges, which are essential for Production Engineering.
Press Tools, also known as Stamping Dies, are crucial in the mass production of metal components through stamping processes. These tools are designed to cut, bend, and shape metal sheets into desired forms, enabling efficient and precise manufacturing of various components.
Moulds, on the other hand, are specialized tools used in the production of plastic and metal components through processes such as injection molding, die casting, and extrusion. These tools are meticulously designed and manufactured to ensure the accurate replication of complex shapes and geometries, making them indispensable in industries like automotive, consumer goods, and electronics.
Jigs and Fixtures are essential tools used to precisely locate and hold workpieces during manufacturing operations, ensuring consistent and accurate positioning. These tools play a critical role in maintaining quality standards and improving efficiency in production processes.
Gauges are precision measuring instruments used to verify the dimensional accuracy of components and ensure they meet the required specifications. They are vital in quality control processes and help maintain tight tolerances in manufacturing.
With the advent of digital manufacturing, the scope of tool engineering has expanded immensely. Today, professionals in this field must not only have a strong foundation in traditional manufacturing practices but also be adept in digital technologies.
Digital Manufacturing: The New Frontier
The landscape of manufacturing is in a perpetual state of evolution, with digital manufacturing emerging as the most innovative and efficient method to bring ideas to life. There are three primary technologies paving the way in this domain. Additive Manufacturing, often referred to as 3D printing, involves building objects layer by layer, utilizing a variety of technologies. Another pivotal technology is CNC (Computer Numerical Control), a process where computers control the precise cutting and shaping of materials.
The Convergence of Tool Engineering and Digital Manufacturing
Tool Engineering and Digital Manufacturing represent the intersection of traditional manufacturing practices and modern technological innovations, forming a hybrid field that is reshaping the industrial landscape. The integration of tool engineering with digital manufacturing opens new avenues for professionals in the industry. For example, someone with a diploma in tool and die engineering can work seamlessly in both traditional and digital manufacturing settings, applying their expertise to improve tool design using digital simulations and prototyping.
NTTF: Bridging the Gap Between Tradition and Innovation
For those interested in pursuing a career in this dynamic field, obtaining a diploma in tool engineering or a tool engineering diploma can provide a solid foundation. One exemplary program that aspiring tool engineers should consider is the Tool Engineering Diploma offered by NTTF (Nettur Technical Training Foundation). Nettur Technical Training Institute’s diploma program is renowned for its comprehensive curriculum that blends both traditional tool engineering principles and modern digital techniques. With a focus on both theoretical knowledge and practical application, NTTF’s Tool Engineering Diploma equips students with the skills necessary to thrive in both conventional and modern manufacturing environments.
At NTTF, these cutting-edge digital manufacturing techniques are at the core of the educational offerings in tool engineering. The programs are meticulously designed to foster comprehensive development, making our graduates highly skilled and employable in the fields of Tool and Die Making and Digital Manufacturing. Under the expert guidance of dedicated instructors, students gain hands-on experience with the latest technologies, preparing them to excel in this rapidly advancing industry.
Integration in Education and Training
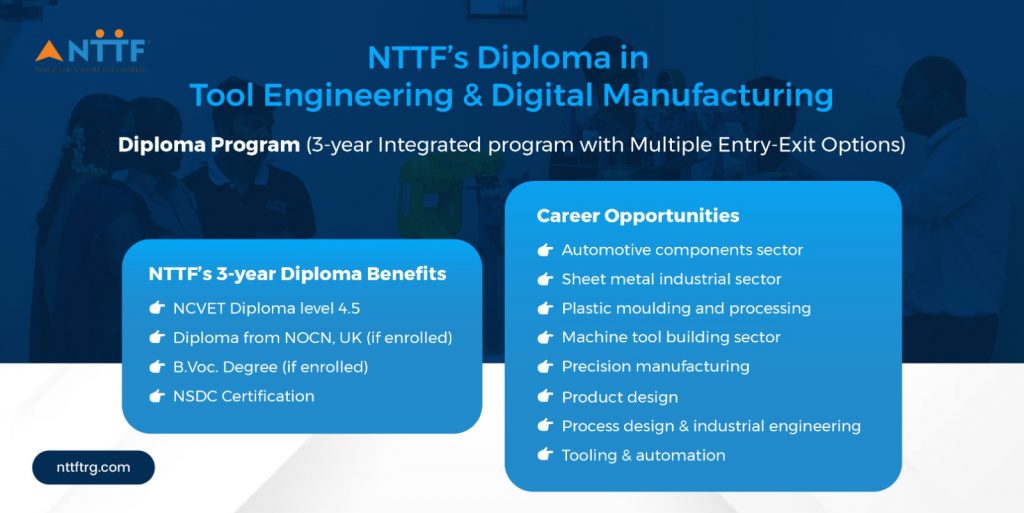
Educational institutions like NTTF are integrating these advanced digital manufacturing techniques into their tool engineering curricula. By doing so, they prepare students not only to understand but also to innovate within this evolving field. Courses combine theoretical knowledge with practical application, providing a well-rounded foundation in both the art of traditional tool design and the science of digital processes.
Here are some key features of NTTF’s Diploma in Tool Engineering & Digital Manufacturing:
- Multiple Entry-Exit Models: NTTF provides flexibility with multiple entry and exit points during the course, catering to individual learning needs and schedules.
- Industry-Relevant Curriculum: The curriculum is designed to match current industry demands, ensuring practical skills and knowledge applicable to real-world scenarios.
- International Accreditation: NTTF’s diploma programs are internationally accredited by NOCN UK.
- State-of-the-Art Facilities: NTTF offers cutting-edge infrastructure and resources to create an optimal learning environment for students.
- Placement Assistance: Dedicated support and guidance are provided to help students secure promising job opportunities after completing the course.
The Future of Tool Engineering & Digital Manufacturing
As the industry continues to evolve, the future of Tool Engineering & Digital Manufacturing looks promising. Innovations such as 3D printing, AI, and IoT are set to revolutionize the way tools are designed and manufactured. Professionals equipped with the right skills, such as those from a CNC machine operator training or a diploma in tool and die engineering, will be well-positioned to lead these advancements.
Moreover, the ongoing digital transformation in manufacturing will likely create numerous job opportunities, particularly for those who are skilled in both traditional tool engineering and digital manufacturing techniques. The blend of these skills enables professionals to adapt to and thrive in a rapidly changing industrial landscape.
Charting a Future in Tool Engineering & Digital ManufacturingThe integration of Tool Engineering & Digital Manufacturing represents a significant shift in how products are designed and produced. It combines the art of traditional manufacturing with the science of digital technology, creating a multidisciplinary field with immense potential. For those interested in a career that embraces innovation, pursuing education and training in this area, such as a diploma in tool and die engineering or CNC machine operator course, could be the key to unlocking numerous opportunities in the evolving world of manufacturing.